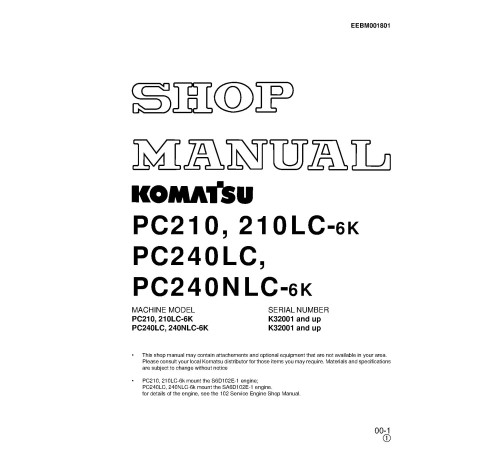
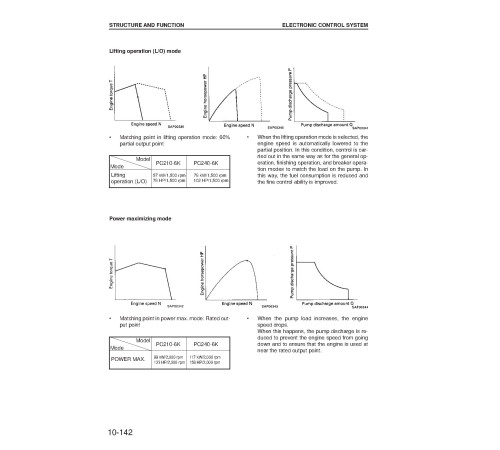
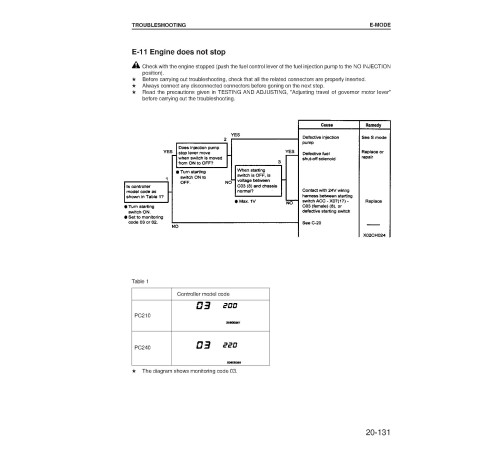
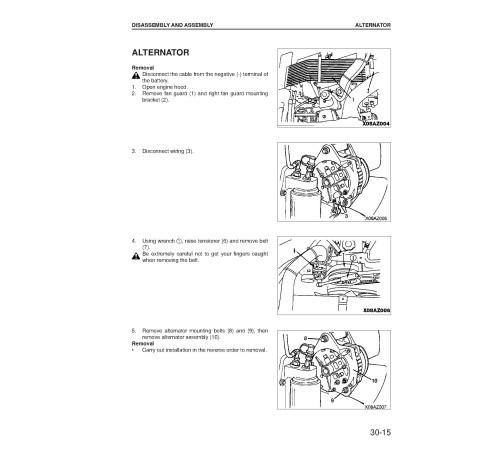




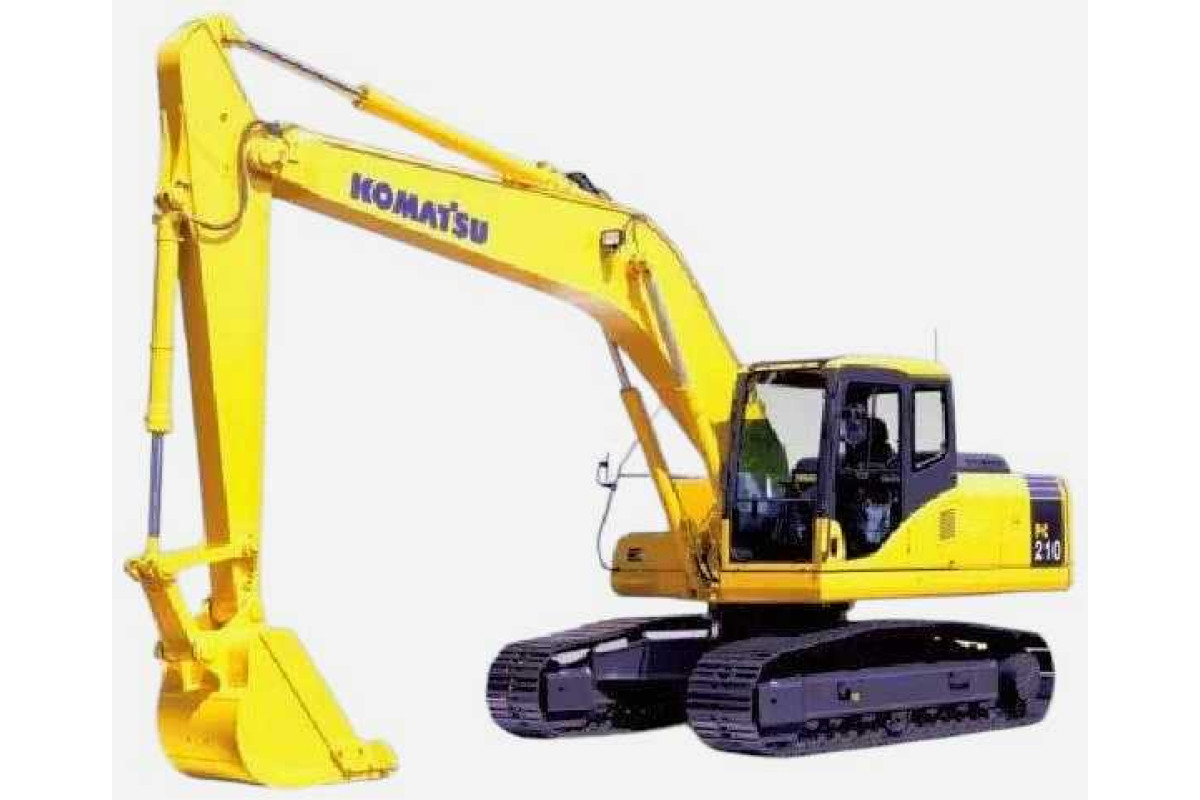
Model
EEBM001801SKU
40083Brand
KomatsuAvailability:
Ready for Instant DownloadThis manual does not contain engine information. Depending on the engine used, see the manuals: S6D102E-1, SA6D102E-1: SEBM010023
$25.00
Language
EnglishModel of Truck
PC210-6K, PC210LC-6K, PC240LC-6K, PC240NLC-6KRegion
United KingdomType of Document
Workshop ManualType of Truck
Crawler ExcavatorIllustrated factory Workshop Manual for Komatsu Crawler Excavators Models PC210-6K, PC210LC-6K, PC240LC-6K and PC240NLC-6K.
This manual will assist you in diagnosing, repairing, and adjusting for your crawler excavator.
You can use a Windows, Mac, or Android device to view this manual. You only need to have a PDF reader installed.
Covered Models (United Kingdom):
PC210-6K (SN: K32001-)
PC210LC-6K (SN: K32001-)
PC240LC-6K (SN: K32001-)
PC240NLC-6K (SN: K32001-)
Format: PDF, 665 pages
Language: English
Table of Contents:
STRUCTURE AND FUNCTION
ENGINE RELATED PARTS
RADIATOR OIL COOLER
POWER TRAIN
FINAL DRIVE
SWING CIRCLE
SWING MACHINERY
TRACK FRAME, RECOIL SPRING
TRACK SHOE
HYDRAULIC TANK
HYDRAULIC PUMP
CONTROL VALVE
SAFETY- SUCTION VALVE FOR SERVICE VALVE
SELF- REDUCING PRESSURE VALVE
CLSS
SWING MOTOR
CENTER SWIVEL JOINT TRAVEL MOTOR
VALVE CONTROL WORK EQUIPMENT SWING PPC VALVE
TRAVEL PPC VALVE
SERVICE PPC VALVE
SAFETY LOCK VALVE PPC ACCUMULATOR STRAIGHT- TRAVEL SYSTEM
EPC SOLENOID VALVE
OVERLOAD WARNING DEVICE
HOSE BURST PROTECTION VALVE (BOOM)
WORK EQUIPMENT ENGINE CONTROL SYSTEM
ELECTRONIC CONTROL SYSTEM
MACHINE MONITOR SYSTEM
TESTING AND ADJUSTING
TESTING AND ADJUSTING STANDARD VALUE TABLE
STANDARD VALUE TABLE FOR ELECTRICAL PARTS
MEASURING ENGINE SPEED
MEASURING EXHAUST GAS COLOR
ADJUSTING VALVE CLEARANCE
MEASURING COMPRESSION PRESSURE
MEASURING BLOW- BY PRES-SURE
TESTING AND ADJUSTING FUEL INJECTION TIMING
MEASURE ENGINE OIL PRESSURE
TESTING AND ADJUSTING FAN BELT TENSION
MEASURING SPEED SENSOR
TESTING AND ADJUSTING GOV-ERNOR MOTOR LEVER STROKE
TESTING AND ADJUSTING HYDRAULIC PRESSURE IN WORK EQUIPMENT, SWING AND TRAVEL CIRCUIT
TESTING AND ADJUSTING PC VALVE OUTPUT PRESSURE (SERVO PISTON INPUT PRES-SURE)
TESTING AND ADJUSTING LS VALVE OUTPUT PRESSURE (SERVO PISTON INPUT PRESSURE AND LS DIFFERENTIAL PRESSURE)
TESTING AND ADJUSTING CONTROL CIRCUIT OIL PRESSURE
TESTING SOLENOID VALVE OUT-PUT PRESSURE
MEASURING PPC VALVE OUTPUT PRESSURE
ADJUSTING WORK EQUIPMENT SWING PPC VALVE
ADJUSTMENT OF FLOW CON-TROL SYSTEM
Graph of PPC Pressure Against HCU Circuit Oil Flow
TESTING TRAVEL DEVIATION
TESTING LOCATIONS CAUSING HYDRAULIC DRIFT OF WORK EQUIPMENT
MEASURE OIL LEAKAGE
RELEASING REMAINING PRESSURE IN HYDRAULIC CIRCUIT
TESTING CLEARANCE OF SWING CIRCLE BEARING
TESTING AND ADJUSTING TRACK SHOE TENSION
BLEEDING AIR
SEQUENCE OF EVENTS IN TROUBLESHOOTING
POINTS TO REMEMBER WHEN CARRYING OUT MAINTENANCE
CHECKS BEFORE TROUBLESHOOTING
CONNECTOR TYPES AND MOUNTING LOCATIONS
CONNECTION TABLE FOR CONNECTOR PIN NUMBERS
EXPLANATION OF CONTROL MECHANISM FOR ELECTRICAL SYSTEM
DISPLAY METHOD AND SPECIAL FUNCTIONS OF MONITOR PANEL
METHOD OF USING JUDGEMENT TABLE
METHOD OF USING TROUBLESHOOTING CHARTS
DETAILS OF TROUBLESHOOTING AND TROUBLESHOOTING PROCEDURE
SERVICE CODE TABLE
TROUBLESHOOTING OF COMMUNICATION ABNORMALITY SYSTEM (N MODE)
TROUBLESHOOTING OF ENGINE THROTTLE PUMP CONTROLLER (GOVERNOR CONTROL SYSTEM) (E MODE)
ACTION TAKEN BY CONTROLLER WHEN ABNORMALITY OCCURS AND PROBLEMS ON MACHINE
JUDGEMENT TABLE FOR ENGINE THROTTLE PUMP GOVERNOR (GOVERNOR CONTROL SYSTEM) AND ENGINE RELATED PARTS
ELECTRICAL CIRCUIT DIAGRAM FOR E MODE SYSTEM
E- 1 Abnormality in engine throttle pump controller power source (controller LED is OFF)
E- 2 [E308] Abnormality in fuel control dial input value is displayed
E- 3 [E317] Abnormality (disconnection) in motor drive system is displayed
E- 4 [E318] Abnormality (short circuit) in motor drive system is displayed
E- 5 [E306] Abnormality in feedback potentiometer system is displayed
E- 6 [E315] Abnormality (short circuit) in battery relay output system is displayed
E- 7 [E316] Abnormality (step- out) in motor is displayed
E- 8 Engine does not start
TROUBLESHOOTING OF ENGINE SYSTEM (S MODE)
TROUBLESHOOTING OF ENGINE THROTTLE PUMP CONTROLLER (PUMP CONTROL SYSTEM) (C- MODE)
ACTION TAKEN BY CONTROLLER WHEN ABNORMALITY OCCURS AND PROBLEMS ON MACHINE
JUDGEMENT TABLE FOR ENGINE THROTTLE PUMP CONTROLLER (PUMP CONTROL SYSTEM) AND HYDRAULIC RELATED PARTS ELECTICAL CIRCUIT DIAGRAM FOR C MODE AND F MODE
C- 1 Abnormality in controller power source system (controller LED is OFF)
C- 2 [E232] Short circuit in pump EPC solenoid system is displayed
C- 3 [E233] Disconnection in PC- EPC solenoid system is displayed
C- 4 [213] Disconnection in swing holding brake solenoid system is displayed
C- 5 [E203] Short circuit in swing holding brake solenoid system is displayed
C- 6 [E204] Short circuit in pump merge/ divider solenoid system is displayed
C- 7 [E214] Disconnection in pum merge/ divider solenoid system is displayed
C- 8 [E207] Short circuit in active mode solenoid system is displayed
C- 9 [E208] Disconnection in active mode solenoid system is displayed
C- 10 [E206] Short circuit in travel speed solenoid system is displayed
C- 13 [E215] Disconnection in 2- stage relief solenoid system is displayed
C- 14 [E217] Model selection input error is displayed
C- 15 [E222] Short circuit in LS- EPC solenoid system is displayed
C- 16 [E223] Disconnection in LS- EPC solenoid system is displayed
C- 17 [E224] Abnormality in front pump pressure sensor system is displayed
C- 18 [E225] Abnormality in rear pump pressure sensor system is displayed
C- 19 [E226] Abnormality in pressure sensor power source system is displayed
C- 20 [E227] Abnormality in engine speed sensor system is displayed
TROUBLESHOOTING OF ENGINE THROTTLE PUMP CONTROLLER (INPUT SIGNAL SYSTEM) (F MODE)
F- 2 Bit pattern 20-( 2) Travel oil pressure switch does not light up
F- 3 Bit pattern 20-( 3) Boom LOWER oil pressure switch does not light up
F- 4 Bit pattern 20-( 4) Boom RAISE oil pressure switch does not light up
F- 5 Bit pattern 20-( 5) Arm IN oil pressure switch does not light up
F- 6 Bit pattern 20-( 6) Arm OUT oil pressure switch does not light up
F- 7 Bit pattern 21-( 1) Bucket CURL oil pressure switch does not light up
F- 8 Bit pattern 21-( 2) Bucket DUMP oil pressure switch does not light up
F- 9 Bit pattern 21-( 3) Swing lock switch does not light up
F- 10 Bit pattern 22-( 5) Kerosene mode connection does not light up
F- 11 Bit pattern 22-( 6) L. H. knob switch does not light up
TROUBLESHOOTING OF HYDRAULIC AND MECHANICAL SYSTEM (H- MODE)
PUMP MERGE/ DIVIDER LOGIC
SOLENOID ACTUATION TABLE
H- 1 Speeds of all work equipment, swing, travel are slow
H- 3 No work equipment, travel, swing move H- 2 There is excessive drop in engine speed, or engine stalls
H- 4 Abnormal noise generated (around pump)
H- 5 Auto- deceleration does not work (when PPC shuttle valve)
H- 6 Fine control ability is poor or response is poor
H- 7 Boom is slow or lacks power
H- 8 Arm is slow or lacks power
H- 9 Bucket is slow or lacks power
H- 10 Work equipment (boom, arm, bucket) does not move (but travel and swing are normal)
H- 11 Excessive hydraulic drift (boom, arm, bucket)
H- 12 Excessive time lag (engine at low idling)
H- 13 Other equipment moves when single circuit is relieved
M- 30 Related electric circuit diagram H- 14 Lack of power when pressure rises
H- 16 In compound operations, work equipment with larger load is slow
H- 15 In L/ O, F/ O modes, work equipment speed is faster than specified speed
H- 17 In swing + boom RAISE, boom RAISE is slow
H- 18 In swing + travel, travel speed drops excessively
H- 19 Travel deviation
H- 20 Travel speed is slow
H- 21 Steering does not turn easily or lacks power
H- 23 Travel does not move (one side only)
H- 22 Travel speed does not switch or is faster than specified speed
H- 24 Does not swing
H- 25 Swing acceleration is poor or swing speed is slow
H- 26 Excessive overrun when stopping swing
H- 27 Excessive shock when stopping wing (one direction only) H- 28 Excessive abnormal noise when stopping swing
H- 29 Excessive hydraulic drift of swing
H- 30 Swing speed is faster than specified speed in L/ O and F/ O modes
TROUBLESHOOTING OF MACHINE MONITOR SYSTEM (M CODE )
ELECTRICAL CIRCUIT DIAGRAM FOR M MODE SYSTEM M- 1 [E101] Abnormality in error data is displayed [E102] Error in clock data is displayed
M- 2 [E103] Short circuit in buzzer output or contact of 24V wiring harness with buzzer drive harness is displayed
M- 3 [E104] Air clogging detected is displayed
M- 4 [E108] Engine coolant temperature 105 C detected is displayed
M- 5 When starting switch is turned ON, none of the lamps on the monitor panel light up for 3 seconds
M- 6 When starting switch is turned ON, monitor panel lamps all stay lit up and do not go out M- 7 When starting switch is turned ON, items lit up on monitor panel are different from actual machine (model)
M- 8 When starting switch is turned ON (engine stopped), basic check items flashes
M- 9 Preheating is not being used but (preheating monitor) lights up
M- 10 When starting switch is turned ON and engine is started, basic check items flash
M- 11 When starting switch is turned ON (engine stopped), caution items, emergency items flash (battery, engine oil pressure lamps do not light up)
M- 12 When starting switch is turned ON and engine is started, caution items, emergency items flash (then there is no abnormality in engine or items to check before troubleshooting)
M- 13 When starting switch is turned ON (engine stopped), buzzer does not sound for 1 second Caution item flashes but buzzer does not sound
M- 14 No abnormality is displayed on monitor but buzzer sounds
M- 15 Night lighting on monitor panel does not light up (liquid crystal display is normal)
M- 16 Coolant temperature gauge does not rise
M- 17 Coolant temperature gauge does not give any display (none of the gauge lamps light up during operation)
M- 18 Fuel level gauge always displays FULL
M- 19 Fuel level gauge does not give display
M- 20 Swing lock switch is turned ON (LOCK) but (swing lock monitor) does not light up
M- 21 Swing prolix switch is turned ON (prolix), but (swing lock monitor) does not flash
M- 22 Service meter does not advance while engine is running M- 23 When starting switch is at OFF and time switch is pressed, time and service meter are not displayed
M- 24 Defective fuel level sensor system
M- 25 Defective coolant temperature sensor system
M- 26 Defective engine oil sensor system
M- 27 Defective coolant level sensor system
M- 28 Defective hydraulic oil level sensor system
M- 29 Wiper does not work or switch is not being used but wiper is actuated
M- 30 Washer motor does not work, or switch is not being used but washer motor is actuated
DISASSEMBLY AND ASSEMBLY
METHOD OF USING MANUAL
SPECIAL TOOL LIST
SKETCHES OF SPECIAL TOOLS
ALTERNATOR
FUEL INJECTION PUMP
WATER PUMP
NOZZLE HOLDER
TURBOCHARGER
THERMOSTAT
GOVERNOR MOTOR
CYLINDER HEAD ASSEMBLY
RADIATOR HYDRAULIC OIL COOLER
ENGINE, MAIN PUMP
DAMPER
FUEL TANK
CENTER SWIVEL JOINT
FINAL DRIVE
SPROCKET
SWING MOTOR
SWING MACHINERY
REVOLVING FRAME
REMOVAL OF SWING CIRCLE ASSEMBLY
INSTALLATION OF SWING CIRCLE ASSEMBLY
REMOVAL OF IDLER RECOIL SPRING ASSEMBLY
INSTALLATION OF IDLER RECOIL SPRING ASSEMBLY
DISASSEMBLY OF RECOIL SPRING ASSEMBLY
ASSEMBLY OF RECOIL SPRING ASSEMBLY
DISASSEMBLY OF IDLER ASSEMBLY
ASSEMBLY OF IDLER ASSEMBLY
REMOVAL OF TRACK ROLLER ASSEMBLY
INSTALLATION OF TRACK ROLLER ASSEMBLY
DISASSEMBLY OF TRACK ROLLER ASSEMBLY
ASSEMBLY OF TRACK ROLLER ASSEMBLY
REMOVAL OF CARRIER ROLLER ASSEMBLY
INSTALLATION OF CARRIER ROLLER ASSEMBLY
DISASSEMBLY OF CARRIER ROLLER ASSEMBLY
ASSEMBLY OF CARRIER ROLLER ASSEMBLY
REMOVAL OF TRACK SHOE ASSEMBLY
INSTALLATION OF TRACK SHOE ASSEMBLY
HYDRAULIC TANK
MAIN PUMP
MAIN PUMP INPUT SHAFT OIL SEAL
CONTROL VALVE
PUMP MERGE- DIVIDER VALVE
MAIN RELIEF VALVE
PC VALVE
LS VALVE
PC, LS- EPC VALVE
SOLENOID VALVE
REMOVAL OF WORK EQUIPMENT SWING PPC VALVE ASSEMBLY
INSTALLATION OF WORK EQUIPMENT SWING PPC VALVE ASSEMBLY
TRAVEL PPC VALVE
REMOVAL OF BOOM CYLINDER ASSEMBLY
INSTALLATION OF BOOM CYLINDER ASSEMBLY
REMOVAL OF ARM CYLINDER ASSEMBLY
INSTALLATION OF ARM CYLINDER ASSEMBLY
REMOVAL OF BUCKET CYLINDER ASSEMBLY
INSTALLATION OF BUCKET CYLINDER ASSEMBLY
DISASSEMBLY OF HYDRAULIC CYLINDER ASSEMBLY
ASSEMBLY OF HYDRAULIC CYLINDER ASSEMBLY
WORK EQUIPMENT
BUCKET
ARM
BUCKET - ARM
BOOM
REMOVAL OF OPERATORS CAB ASSEMBLY
INSTALLATION OF OPERATORS CAB ASSEMBLY
COUNTERWEIGHT
REMOVAL OF ENGINE THROTTLE CONTROLLER ASSEMBLY
MONITOR
MAINTENANCE STANDARD
SWING MACHINERY
SWING CIRCLE FINAL DRIVE
TRACK FRAME, RECOIL SPRING
IDLER
CARRIER ROLLER
TRACK ROLLER
TRACK SHOE
HYDRAULIC PUMP
CONTROL VALVE
VARIABLE PRESSURE COMPENSATION VALVE
SAFETY- SUCTION VALVE FOR SERVICE VALVE
SELF- REDUCING PRESSURE VALVE
SWING MOTOR
TRAVEL MOTOR
TRAVEL PPC VALVE WORK EQUIPMENT SWING PPC VALVE EPC SOLENOID VALVE
CENTER SWIVEL JOINT HYDRAULIC CYLINDER
WORK EQUIPMENT DIMENSIONS OF WORK EQUIPMENT
This manual will assist you in diagnosing, repairing, and adjusting for your crawler excavator.
You can use a Windows, Mac, or Android device to view this manual. You only need to have a PDF reader installed.
Covered Models (United Kingdom):
PC210-6K (SN: K32001-)
PC210LC-6K (SN: K32001-)
PC240LC-6K (SN: K32001-)
PC240NLC-6K (SN: K32001-)
Format: PDF, 665 pages
Language: English
Table of Contents:
STRUCTURE AND FUNCTION
ENGINE RELATED PARTS
RADIATOR OIL COOLER
POWER TRAIN
FINAL DRIVE
SWING CIRCLE
SWING MACHINERY
TRACK FRAME, RECOIL SPRING
TRACK SHOE
HYDRAULIC TANK
HYDRAULIC PUMP
CONTROL VALVE
SAFETY- SUCTION VALVE FOR SERVICE VALVE
SELF- REDUCING PRESSURE VALVE
CLSS
SWING MOTOR
CENTER SWIVEL JOINT TRAVEL MOTOR
VALVE CONTROL WORK EQUIPMENT SWING PPC VALVE
TRAVEL PPC VALVE
SERVICE PPC VALVE
SAFETY LOCK VALVE PPC ACCUMULATOR STRAIGHT- TRAVEL SYSTEM
EPC SOLENOID VALVE
OVERLOAD WARNING DEVICE
HOSE BURST PROTECTION VALVE (BOOM)
WORK EQUIPMENT ENGINE CONTROL SYSTEM
ELECTRONIC CONTROL SYSTEM
MACHINE MONITOR SYSTEM
TESTING AND ADJUSTING
TESTING AND ADJUSTING STANDARD VALUE TABLE
STANDARD VALUE TABLE FOR ELECTRICAL PARTS
MEASURING ENGINE SPEED
MEASURING EXHAUST GAS COLOR
ADJUSTING VALVE CLEARANCE
MEASURING COMPRESSION PRESSURE
MEASURING BLOW- BY PRES-SURE
TESTING AND ADJUSTING FUEL INJECTION TIMING
MEASURE ENGINE OIL PRESSURE
TESTING AND ADJUSTING FAN BELT TENSION
MEASURING SPEED SENSOR
TESTING AND ADJUSTING GOV-ERNOR MOTOR LEVER STROKE
TESTING AND ADJUSTING HYDRAULIC PRESSURE IN WORK EQUIPMENT, SWING AND TRAVEL CIRCUIT
TESTING AND ADJUSTING PC VALVE OUTPUT PRESSURE (SERVO PISTON INPUT PRES-SURE)
TESTING AND ADJUSTING LS VALVE OUTPUT PRESSURE (SERVO PISTON INPUT PRESSURE AND LS DIFFERENTIAL PRESSURE)
TESTING AND ADJUSTING CONTROL CIRCUIT OIL PRESSURE
TESTING SOLENOID VALVE OUT-PUT PRESSURE
MEASURING PPC VALVE OUTPUT PRESSURE
ADJUSTING WORK EQUIPMENT SWING PPC VALVE
ADJUSTMENT OF FLOW CON-TROL SYSTEM
Graph of PPC Pressure Against HCU Circuit Oil Flow
TESTING TRAVEL DEVIATION
TESTING LOCATIONS CAUSING HYDRAULIC DRIFT OF WORK EQUIPMENT
MEASURE OIL LEAKAGE
RELEASING REMAINING PRESSURE IN HYDRAULIC CIRCUIT
TESTING CLEARANCE OF SWING CIRCLE BEARING
TESTING AND ADJUSTING TRACK SHOE TENSION
BLEEDING AIR
SEQUENCE OF EVENTS IN TROUBLESHOOTING
POINTS TO REMEMBER WHEN CARRYING OUT MAINTENANCE
CHECKS BEFORE TROUBLESHOOTING
CONNECTOR TYPES AND MOUNTING LOCATIONS
CONNECTION TABLE FOR CONNECTOR PIN NUMBERS
EXPLANATION OF CONTROL MECHANISM FOR ELECTRICAL SYSTEM
DISPLAY METHOD AND SPECIAL FUNCTIONS OF MONITOR PANEL
METHOD OF USING JUDGEMENT TABLE
METHOD OF USING TROUBLESHOOTING CHARTS
DETAILS OF TROUBLESHOOTING AND TROUBLESHOOTING PROCEDURE
SERVICE CODE TABLE
TROUBLESHOOTING OF COMMUNICATION ABNORMALITY SYSTEM (N MODE)
TROUBLESHOOTING OF ENGINE THROTTLE PUMP CONTROLLER (GOVERNOR CONTROL SYSTEM) (E MODE)
ACTION TAKEN BY CONTROLLER WHEN ABNORMALITY OCCURS AND PROBLEMS ON MACHINE
JUDGEMENT TABLE FOR ENGINE THROTTLE PUMP GOVERNOR (GOVERNOR CONTROL SYSTEM) AND ENGINE RELATED PARTS
ELECTRICAL CIRCUIT DIAGRAM FOR E MODE SYSTEM
E- 1 Abnormality in engine throttle pump controller power source (controller LED is OFF)
E- 2 [E308] Abnormality in fuel control dial input value is displayed
E- 3 [E317] Abnormality (disconnection) in motor drive system is displayed
E- 4 [E318] Abnormality (short circuit) in motor drive system is displayed
E- 5 [E306] Abnormality in feedback potentiometer system is displayed
E- 6 [E315] Abnormality (short circuit) in battery relay output system is displayed
E- 7 [E316] Abnormality (step- out) in motor is displayed
E- 8 Engine does not start
TROUBLESHOOTING OF ENGINE SYSTEM (S MODE)
TROUBLESHOOTING OF ENGINE THROTTLE PUMP CONTROLLER (PUMP CONTROL SYSTEM) (C- MODE)
ACTION TAKEN BY CONTROLLER WHEN ABNORMALITY OCCURS AND PROBLEMS ON MACHINE
JUDGEMENT TABLE FOR ENGINE THROTTLE PUMP CONTROLLER (PUMP CONTROL SYSTEM) AND HYDRAULIC RELATED PARTS ELECTICAL CIRCUIT DIAGRAM FOR C MODE AND F MODE
C- 1 Abnormality in controller power source system (controller LED is OFF)
C- 2 [E232] Short circuit in pump EPC solenoid system is displayed
C- 3 [E233] Disconnection in PC- EPC solenoid system is displayed
C- 4 [213] Disconnection in swing holding brake solenoid system is displayed
C- 5 [E203] Short circuit in swing holding brake solenoid system is displayed
C- 6 [E204] Short circuit in pump merge/ divider solenoid system is displayed
C- 7 [E214] Disconnection in pum merge/ divider solenoid system is displayed
C- 8 [E207] Short circuit in active mode solenoid system is displayed
C- 9 [E208] Disconnection in active mode solenoid system is displayed
C- 10 [E206] Short circuit in travel speed solenoid system is displayed
C- 13 [E215] Disconnection in 2- stage relief solenoid system is displayed
C- 14 [E217] Model selection input error is displayed
C- 15 [E222] Short circuit in LS- EPC solenoid system is displayed
C- 16 [E223] Disconnection in LS- EPC solenoid system is displayed
C- 17 [E224] Abnormality in front pump pressure sensor system is displayed
C- 18 [E225] Abnormality in rear pump pressure sensor system is displayed
C- 19 [E226] Abnormality in pressure sensor power source system is displayed
C- 20 [E227] Abnormality in engine speed sensor system is displayed
TROUBLESHOOTING OF ENGINE THROTTLE PUMP CONTROLLER (INPUT SIGNAL SYSTEM) (F MODE)
F- 2 Bit pattern 20-( 2) Travel oil pressure switch does not light up
F- 3 Bit pattern 20-( 3) Boom LOWER oil pressure switch does not light up
F- 4 Bit pattern 20-( 4) Boom RAISE oil pressure switch does not light up
F- 5 Bit pattern 20-( 5) Arm IN oil pressure switch does not light up
F- 6 Bit pattern 20-( 6) Arm OUT oil pressure switch does not light up
F- 7 Bit pattern 21-( 1) Bucket CURL oil pressure switch does not light up
F- 8 Bit pattern 21-( 2) Bucket DUMP oil pressure switch does not light up
F- 9 Bit pattern 21-( 3) Swing lock switch does not light up
F- 10 Bit pattern 22-( 5) Kerosene mode connection does not light up
F- 11 Bit pattern 22-( 6) L. H. knob switch does not light up
TROUBLESHOOTING OF HYDRAULIC AND MECHANICAL SYSTEM (H- MODE)
PUMP MERGE/ DIVIDER LOGIC
SOLENOID ACTUATION TABLE
H- 1 Speeds of all work equipment, swing, travel are slow
H- 3 No work equipment, travel, swing move H- 2 There is excessive drop in engine speed, or engine stalls
H- 4 Abnormal noise generated (around pump)
H- 5 Auto- deceleration does not work (when PPC shuttle valve)
H- 6 Fine control ability is poor or response is poor
H- 7 Boom is slow or lacks power
H- 8 Arm is slow or lacks power
H- 9 Bucket is slow or lacks power
H- 10 Work equipment (boom, arm, bucket) does not move (but travel and swing are normal)
H- 11 Excessive hydraulic drift (boom, arm, bucket)
H- 12 Excessive time lag (engine at low idling)
H- 13 Other equipment moves when single circuit is relieved
M- 30 Related electric circuit diagram H- 14 Lack of power when pressure rises
H- 16 In compound operations, work equipment with larger load is slow
H- 15 In L/ O, F/ O modes, work equipment speed is faster than specified speed
H- 17 In swing + boom RAISE, boom RAISE is slow
H- 18 In swing + travel, travel speed drops excessively
H- 19 Travel deviation
H- 20 Travel speed is slow
H- 21 Steering does not turn easily or lacks power
H- 23 Travel does not move (one side only)
H- 22 Travel speed does not switch or is faster than specified speed
H- 24 Does not swing
H- 25 Swing acceleration is poor or swing speed is slow
H- 26 Excessive overrun when stopping swing
H- 27 Excessive shock when stopping wing (one direction only) H- 28 Excessive abnormal noise when stopping swing
H- 29 Excessive hydraulic drift of swing
H- 30 Swing speed is faster than specified speed in L/ O and F/ O modes
TROUBLESHOOTING OF MACHINE MONITOR SYSTEM (M CODE )
ELECTRICAL CIRCUIT DIAGRAM FOR M MODE SYSTEM M- 1 [E101] Abnormality in error data is displayed [E102] Error in clock data is displayed
M- 2 [E103] Short circuit in buzzer output or contact of 24V wiring harness with buzzer drive harness is displayed
M- 3 [E104] Air clogging detected is displayed
M- 4 [E108] Engine coolant temperature 105 C detected is displayed
M- 5 When starting switch is turned ON, none of the lamps on the monitor panel light up for 3 seconds
M- 6 When starting switch is turned ON, monitor panel lamps all stay lit up and do not go out M- 7 When starting switch is turned ON, items lit up on monitor panel are different from actual machine (model)
M- 8 When starting switch is turned ON (engine stopped), basic check items flashes
M- 9 Preheating is not being used but (preheating monitor) lights up
M- 10 When starting switch is turned ON and engine is started, basic check items flash
M- 11 When starting switch is turned ON (engine stopped), caution items, emergency items flash (battery, engine oil pressure lamps do not light up)
M- 12 When starting switch is turned ON and engine is started, caution items, emergency items flash (then there is no abnormality in engine or items to check before troubleshooting)
M- 13 When starting switch is turned ON (engine stopped), buzzer does not sound for 1 second Caution item flashes but buzzer does not sound
M- 14 No abnormality is displayed on monitor but buzzer sounds
M- 15 Night lighting on monitor panel does not light up (liquid crystal display is normal)
M- 16 Coolant temperature gauge does not rise
M- 17 Coolant temperature gauge does not give any display (none of the gauge lamps light up during operation)
M- 18 Fuel level gauge always displays FULL
M- 19 Fuel level gauge does not give display
M- 20 Swing lock switch is turned ON (LOCK) but (swing lock monitor) does not light up
M- 21 Swing prolix switch is turned ON (prolix), but (swing lock monitor) does not flash
M- 22 Service meter does not advance while engine is running M- 23 When starting switch is at OFF and time switch is pressed, time and service meter are not displayed
M- 24 Defective fuel level sensor system
M- 25 Defective coolant temperature sensor system
M- 26 Defective engine oil sensor system
M- 27 Defective coolant level sensor system
M- 28 Defective hydraulic oil level sensor system
M- 29 Wiper does not work or switch is not being used but wiper is actuated
M- 30 Washer motor does not work, or switch is not being used but washer motor is actuated
DISASSEMBLY AND ASSEMBLY
METHOD OF USING MANUAL
SPECIAL TOOL LIST
SKETCHES OF SPECIAL TOOLS
ALTERNATOR
FUEL INJECTION PUMP
WATER PUMP
NOZZLE HOLDER
TURBOCHARGER
THERMOSTAT
GOVERNOR MOTOR
CYLINDER HEAD ASSEMBLY
RADIATOR HYDRAULIC OIL COOLER
ENGINE, MAIN PUMP
DAMPER
FUEL TANK
CENTER SWIVEL JOINT
FINAL DRIVE
SPROCKET
SWING MOTOR
SWING MACHINERY
REVOLVING FRAME
REMOVAL OF SWING CIRCLE ASSEMBLY
INSTALLATION OF SWING CIRCLE ASSEMBLY
REMOVAL OF IDLER RECOIL SPRING ASSEMBLY
INSTALLATION OF IDLER RECOIL SPRING ASSEMBLY
DISASSEMBLY OF RECOIL SPRING ASSEMBLY
ASSEMBLY OF RECOIL SPRING ASSEMBLY
DISASSEMBLY OF IDLER ASSEMBLY
ASSEMBLY OF IDLER ASSEMBLY
REMOVAL OF TRACK ROLLER ASSEMBLY
INSTALLATION OF TRACK ROLLER ASSEMBLY
DISASSEMBLY OF TRACK ROLLER ASSEMBLY
ASSEMBLY OF TRACK ROLLER ASSEMBLY
REMOVAL OF CARRIER ROLLER ASSEMBLY
INSTALLATION OF CARRIER ROLLER ASSEMBLY
DISASSEMBLY OF CARRIER ROLLER ASSEMBLY
ASSEMBLY OF CARRIER ROLLER ASSEMBLY
REMOVAL OF TRACK SHOE ASSEMBLY
INSTALLATION OF TRACK SHOE ASSEMBLY
HYDRAULIC TANK
MAIN PUMP
MAIN PUMP INPUT SHAFT OIL SEAL
CONTROL VALVE
PUMP MERGE- DIVIDER VALVE
MAIN RELIEF VALVE
PC VALVE
LS VALVE
PC, LS- EPC VALVE
SOLENOID VALVE
REMOVAL OF WORK EQUIPMENT SWING PPC VALVE ASSEMBLY
INSTALLATION OF WORK EQUIPMENT SWING PPC VALVE ASSEMBLY
TRAVEL PPC VALVE
REMOVAL OF BOOM CYLINDER ASSEMBLY
INSTALLATION OF BOOM CYLINDER ASSEMBLY
REMOVAL OF ARM CYLINDER ASSEMBLY
INSTALLATION OF ARM CYLINDER ASSEMBLY
REMOVAL OF BUCKET CYLINDER ASSEMBLY
INSTALLATION OF BUCKET CYLINDER ASSEMBLY
DISASSEMBLY OF HYDRAULIC CYLINDER ASSEMBLY
ASSEMBLY OF HYDRAULIC CYLINDER ASSEMBLY
WORK EQUIPMENT
BUCKET
ARM
BUCKET - ARM
BOOM
REMOVAL OF OPERATORS CAB ASSEMBLY
INSTALLATION OF OPERATORS CAB ASSEMBLY
COUNTERWEIGHT
REMOVAL OF ENGINE THROTTLE CONTROLLER ASSEMBLY
MONITOR
MAINTENANCE STANDARD
SWING MACHINERY
SWING CIRCLE FINAL DRIVE
TRACK FRAME, RECOIL SPRING
IDLER
CARRIER ROLLER
TRACK ROLLER
TRACK SHOE
HYDRAULIC PUMP
CONTROL VALVE
VARIABLE PRESSURE COMPENSATION VALVE
SAFETY- SUCTION VALVE FOR SERVICE VALVE
SELF- REDUCING PRESSURE VALVE
SWING MOTOR
TRAVEL MOTOR
TRAVEL PPC VALVE WORK EQUIPMENT SWING PPC VALVE EPC SOLENOID VALVE
CENTER SWIVEL JOINT HYDRAULIC CYLINDER
WORK EQUIPMENT DIMENSIONS OF WORK EQUIPMENT
General
Language
EnglishModel of Truck
PC210-6K, PC210LC-6K, PC240LC-6K, PC240NLC-6KRegion
United KingdomType of Document
Workshop ManualType of Truck
Crawler ExcavatorReviews: 0
There are no reviews for this product.
Questions: 0
No questions about this product.